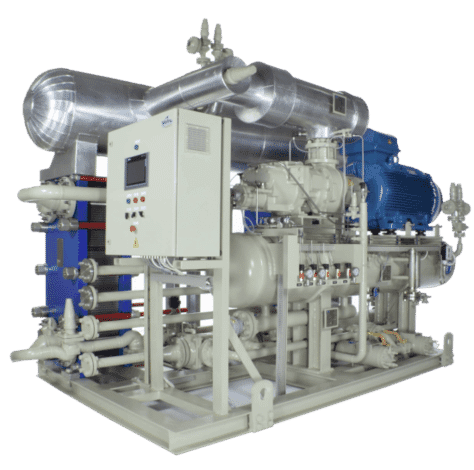
WINTER Industrial Chiller Packages can be used for chilled water, chilled glycol, or chilled brine for many applications in various industries (Food & Beverage, Agro Food, Cold store, Greenhouse, Process Cooling, etc.). While using ammonia (NH3) as a refrigerant, the WINTER Chiller Packages are highly efficient and sustainable. Since NH3 has zero ODP and zero GWP the WINTER Chiller contributes to a green footprint of our client’s project. However, WINTER can provide such Chillers with all other common refrigerants as well. All of the WINTER packages are designed according to the international standards API, ASME, PED, AD 2000, GOST, etc. All the WINTER Chillers can be supplied with different types of condensers (water-cooled, air-cooled, or evaporative air-cooled)
While making the decision for a WINTER Chiller our clients can minimize the installation time and cost within the plant room on site. The Chiller packages can be equipped with a power panel as well so that only the power connection is remaining on site.
Industrial Chiller
An industrial chiller is a type of refrigeration system used to provide cooling for various industrial processes or equipment. It works by circulating chilled water, glycol, or other cooling fluids through a system of heat exchangers or coils, which removes heat from the surrounding environment and lowers its temperature.
The components of an industrial chiller typically include:
- Compressor: This is responsible for compressing the refrigerant gas and raising its temperature and pressure before it enters the condenser.
- Condenser: This is a heat exchanger that removes heat from the refrigerant by condensing it back into a liquid state.
- Evaporator: This is a heat exchanger that removes heat from the surroundings by vaporizing the refrigerant.
- Expansion valve: This is responsible for reducing the pressure of the refrigerant and regulating its flow through the system.
- Control systems: These are the electrical and mechanical systems that control the operation of the chiller and ensure that it operates safely and efficiently.
Industrial chillers can be used in a variety of applications, such as:
- Air conditioning and ventilation systems
- Process cooling for industrial equipment or manufacturing processes
- Medical or laboratory equipment
- Data centers and IT equipment
- Food and beverage processing
Industrial chillers can be categorized into two main types:
- Air-cooled chillers: These chillers use air to remove heat from the refrigerant, which is then discharged to the surrounding environment.
- Water-cooled chillers: These chillers use water to remove heat from the refrigerant, which is then discharged to a cooling tower or another heat-rejection device.
Energy efficiency is an important consideration when choosing and operating an industrial chiller. Energy-saving measures can include selecting a chiller with high-efficiency components, optimizing the operating conditions, and using advanced control systems to minimize energy use.
WINTER offers easy maintenance and proper operation of an industrial chiller for ensuring safe and efficient operation, as well as maximizing its lifespan. This can include tasks such as cleaning the heat exchangers, checking refrigerant levels, and inspecting electrical components.
- WINTER Industrial chillers can be powered by various energy sources, including electricity, natural gas, or diesel fuel. The choice of energy source can impact the operating costs and environmental impact of the chiller.
- WINTER Chillers can be configured in different ways depending on the specific application and cooling requirements. For example, a chiller may have multiple compressors to provide redundancy and ensure reliable operation, or it may be designed to operate at different capacities depending on the cooling load.
APPLICATIONS:
- Cold Storage
- Food & Beverage Industry
- Process Cooling
- Greenhouses
- HVAC